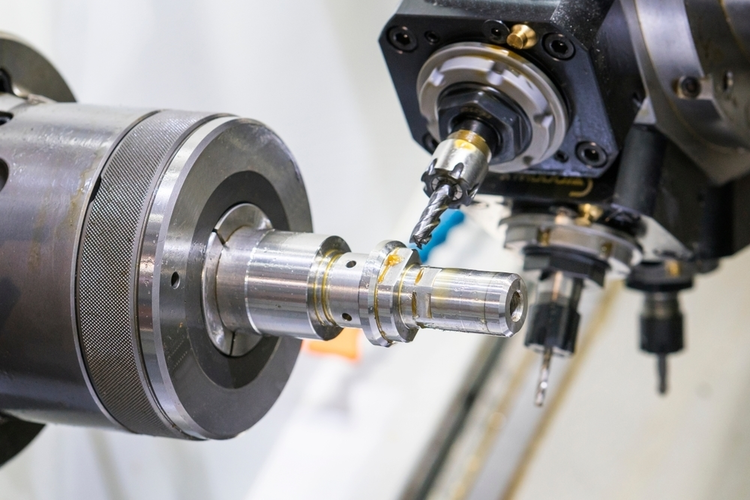
The expanding metal fabrication industry supports almost one and a half million people. Metal components are manipulated, chopped, and put together to form metal structures. The manufacture of car chassis, aircraft fuselage panels, roofing, building panels, and other objects uses custom sheet metal fabrication wilson nc. The bulk relies on three primary processes.
You will discover the three bespoke metal fabrication processes and how they vary from many other forms of fabrication when you continue reading below.
About Custom Metal Fabrication
Metal fabrication is necessary whenever something is made out of metal, yet it may be done with only a portable cutting torch and an arc welder. If you require small metal decorations, steel construction beams, or anything in between, custom metal fabrication is necessary if you require anything made from metal to more exacting specifications.
The term “custom metal fabrication” describes the specialised application of numerous manufacturing techniques to create a product. Custom fabrication, as opposed to ordinary stock metal fabrication techniques, enables the production of application-specific items.
Additionally, based on the application’s requirements, product specifications could vary across the automotive, military, and defence industries.
Metal fabricators must use a flexible manufacturing method to satisfy the needs of these industries. In addition to ensuring lengthy standards and effectiveness, this process enables them to design and develop application-specific products.
3 Processes for Custom Metal Fabrication
These three processes make up a successful outcome for custom metal fabrication. But you can accomplish stainless steel threading with the first two processes, cutting and bending. Here are three approaches to assist you in learning more about customised metal manufacturing processes:
Cutting
To start, the first stage of producing metal is cutting. A new metal construct or product is created throughout this procedure by the metal fabrication firm by cutting pieces of unprocessed metal. Specialised tools are required to cut metal, whether it be iron, aluminium, steel, or any other common metal.
Additionally, some companies that specialise in metal fabrication utilise torches to cut metal, while others use numerically controlled CNC services that use lasers or water jets. When finished, the company will have pristine, precisely proportioned metal sheets or pieces to operate with.
Bending
After being cut, the raw metal must be bent by enterprises that fabricate metal. There are a variety of techniques for bending metal after it has been cut. Some companies that fabricate metal use hammers to form metal sheets or components.
Hammering may be done manually or mechanically in the process of power hammering. Press brakes, however, are now being used by a number of metal manufacturing companies to bend their metal. This enormous piece of industrial machinery mechanically presses metal sheets and components into a precise shape once it is turned on. It forces the metal into the desired shape by clamping it between two punch dies.
Assembling
The last stage of metal production is assembly. As the name implies, this process comprises putting the metal sheet or components together to achieve the desired outcome. The most used technique for assembly is welding. However, you may also use other techniques.
For instance, metal fabrication companies may use glue, fasteners, or screws in addition to welding. After putting the metal together, the business will finish the product and dispatch it to its customers.
Comparison of Custom Metal Fabrication and Stock Fabrication
There are additional benefits to custom metal fabrication over stock fabrication. The recommendation made below may assist you in understanding the benefits of the process:
Higher Efficiency
Combining two or more processes may occasionally result in the creation of a component. The ability to choose the optimum fabrication method from a range of options is provided by custom fabrication. The operational efficiency of custom fabrication is superior to stock fabrication.
Losses brought on by contact, wear, and tear, as well as component overlapping, may be prevented by compatible component creation made possible by custom metal fabrication.
Lifecycle of a Durable Product
Production of durable items is aided by custom fabrication. A fabricator may choose the material that best fits the application after consultation. In addition to the process’s chemical interactions, the fabricator may take into account possible stresses, strains, and external forces.
The outcome is an application-centric product design. Using stainless steel during custom fabrication allows the metal fabricator to increase the product’s shelf life.
Compatibility with High Components
Component compatibility is made possible by customised metal or sheet metal production. All the parts are compatible since they were all created specifically and built to certain requirements. Friction between two components, dimensional fitting, and chemical surface reactivity are important considerations in bespoke manufacturing processes.
Conclusion
The country’s rapidly developing industrial sector heavily depends on custom metal fabrication. Despite using a range of tools and techniques, organisations specialising in metal fabrication must depend on a three-step procedure comprising cutting, bending, and assembly. Metal workers are able to create new goods by using these three processes to transform raw metal resources.