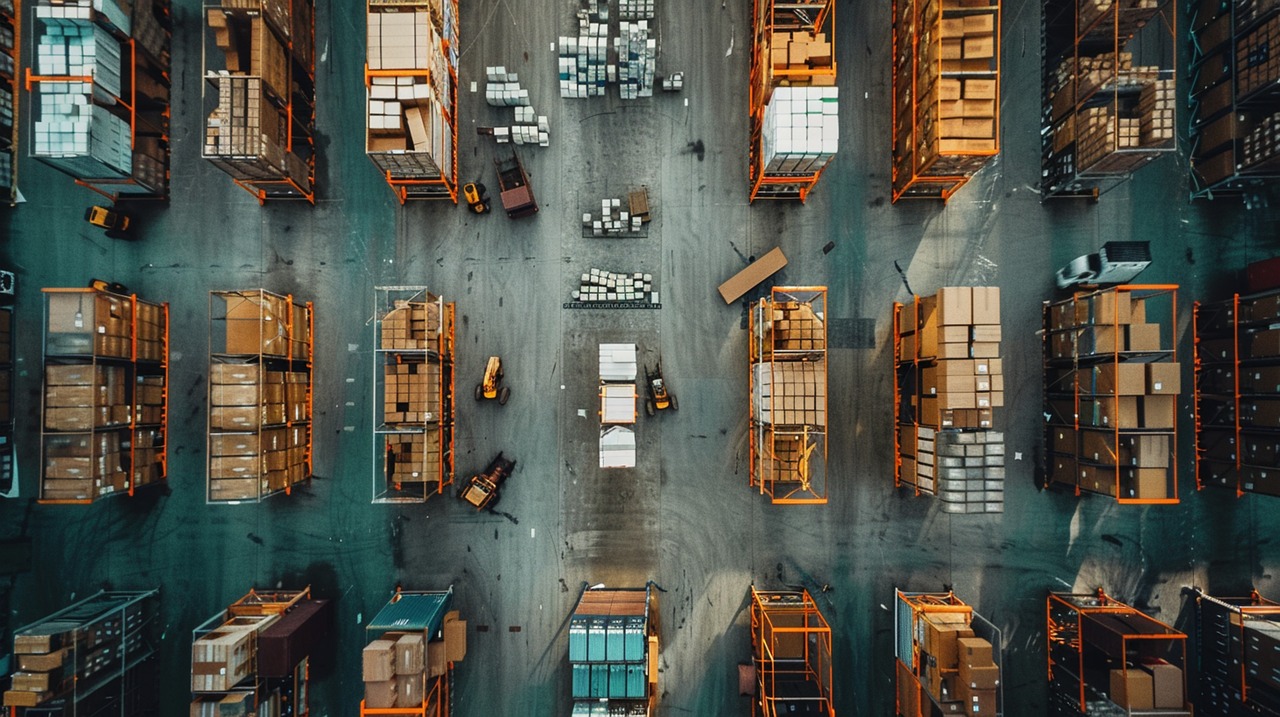
Choosing the right flooring for your warehouse is a critical decision that impacts the safety, efficiency, and longevity of your facility. With various factors to consider—from durability to maintenance requirements—it’s essential to make an informed choice that meets the specific needs of your operations. Here are five comprehensive tips to guide you in selecting the best warehouse flooring.
1. Assess Durability and Load-Bearing Capacity
When selecting industrial flooring UK, one of the primary considerations is the material’s durability and load-bearing capacity. Warehouses are high-traffic environments where floors must endure constant use, heavy machinery, and the weight of stored goods.
Concrete is one of the most popular choices for warehouse flooring due to its high durability and ability to support heavy loads. Reinforced concrete, in particular, can handle the pressure from forklifts, pallets, and other heavy equipment without cracking or deteriorating. Additionally, concrete floors can be enhanced with coatings or sealants to increase their strength and resistance to wear and tear.
Epoxy flooring, another durable option, is known for its strength and resistance to chemicals, making it ideal for warehouses dealing with corrosive substances. Epoxy is applied as a coating over concrete, providing an extra layer of protection and extending the floor’s lifespan.
It’s crucial to evaluate the specific weight loads and traffic patterns in your warehouse to choose a flooring material that can withstand the demands of your operations.
2. Prioritize Safety Features
Safety should be a top priority when selecting warehouse flooring. Slips, trips, and falls are common hazards in warehouses, especially in areas where spills, moisture, or debris are present. To mitigate these risks, it’s important to choose flooring that offers adequate slip resistance.
Textured surfaces or anti-slip coatings can be applied to both concrete and epoxy floors to enhance grip, reducing the likelihood of accidents. In areas where spills are frequent, such as loading docks or chemical storage zones, anti-slip mats or overlays may be added to provide additional protection.
Additionally, consider the use of safety markings or color-coded zones on the flooring to guide workers and enhance safety. These markings can indicate safe walkways, hazardous areas, or equipment zones, helping to prevent accidents and improve overall workflow.
3. Consider Maintenance and Upkeep
The ease of maintenance is another critical factor to consider when choosing warehouse flooring. Warehouses are often busy environments where downtime for maintenance needs to be minimized. Therefore, opting for a low-maintenance flooring option can save both time and money in the long run.
Polished concrete is a popular choice for its minimal maintenance requirements. The polished surface resists stains and can be easily cleaned with regular sweeping and occasional mopping. This type of flooring is also highly durable, reducing the need for frequent repairs or resurfacing.
Epoxy flooring is also relatively low-maintenance, as its smooth, non-porous surface resists stains and spills. However, it’s important to note that epoxy floors can be prone to scratching, so care should be taken when moving heavy machinery or equipment across the surface.
Regular inspections and cleaning are essential to maintaining the longevity of any warehouse flooring. Establish a maintenance schedule that includes routine checks for cracks, wear, and other potential issues, addressing them promptly to prevent larger problems from developing.
4. Evaluate Chemical Resistance
If your warehouse handles chemicals, it’s imperative to select flooring that is resistant to spills and corrosive substances. Chemical exposure can damage certain types of flooring, leading to costly repairs and potentially unsafe conditions.
Epoxy coatings are highly resistant to a wide range of chemicals, making them an excellent choice for warehouses that store or use hazardous materials. The coating creates a protective barrier that prevents chemicals from seeping into the flooring and causing damage.
Sealed concrete is another option that offers chemical resistance. The sealant creates an impermeable layer on the concrete surface, protecting it from chemical spills and making cleanup easier.
When choosing a chemical-resistant flooring option, consider the types of chemicals your warehouse typically handles and consult with flooring specialists to ensure that the selected material meets the necessary safety standards.
5. Plan for Installation Time and Disruption
The installation process is a crucial factor to consider when choosing warehouse flooring. Depending on the material, installation can take anywhere from a few days to several weeks, and it may require your warehouse operations to be temporarily halted or disrupted.
Epoxy flooring generally requires a longer installation time due to the need for multiple layers and curing periods. This process can take up to a week or more, depending on the size of the area and the specific epoxy system used. However, the result is a seamless, durable surface that offers long-term benefits.
Concrete flooring, particularly if it’s already in place, may require less installation time if only a polish or sealant is being applied. However, new concrete installations will require significant time for pouring, setting, and curing.
To minimize disruption, plan the installation during periods of low activity or schedule the work in phases, allowing sections of the warehouse to remain operational while others are being completed.
Conclusion
Choosing the right warehouse flooring is a decision that affects the safety, efficiency, and longevity of your operations. By considering factors such as durability, safety, maintenance, chemical resistance, and installation time, you can make an informed choice that meets the specific needs of your warehouse. Investing in the right flooring solution will not only enhance your warehouse’s functionality but also contribute to a safer and more productive working environment.