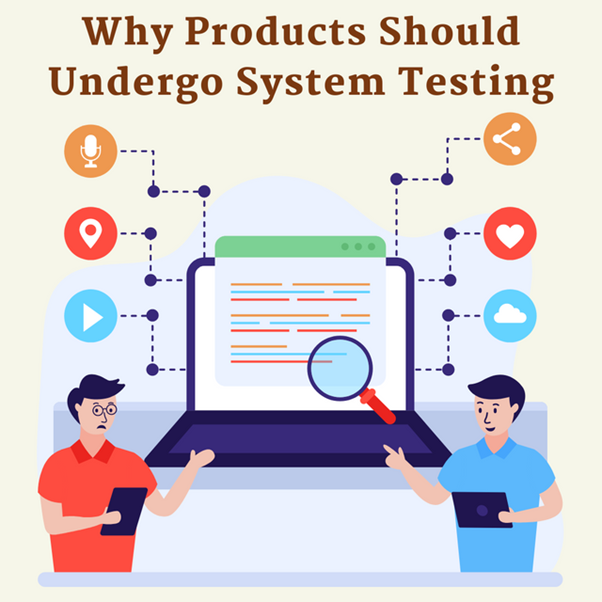
We recognise that teaching transcends technology, and while software can help you manage your training, the success of your company or training department is ultimately determined by the quality of training you provide. That being said, the technology that powers your training operation is critical in determining how effective you can be, how well you understand your performance, and how rapidly you can scale.
The burn-in method is a testing procedure that is used to discover and eliminate defective electronic components before they are sold or incorporated into bigger systems. Burn-in testing is an important aspect for businesses that rely on frequent design modifications and component modification, such as semiconductor production because it aids in maintaining product run homogeneity. Testing procedures such as HTOL testing is designed to highlight potential problems by subjecting products to increased voltage levels, temperatures outside of typical limits, and power cycle circumstances.
A typical burn in testing system consists of a set of sockets that provide a temporary electrical connection between the burn-in board and the device being tested. A normal burn-in board can have up to fifty sockets, and a burn-in system can have several dozen of these boards. A thorough understanding of temperature distributions through the burn-in boards, testing device, and burn-in oven is required for effective burn-in system performance.
Levels of Burn-In Testing
The most frequent levels of burn-in testing for electronic components are die-level, package-level, and wafer-level burn-in. These classifications refer to the stages of production during which the products are evaluated, and each may provide manufacturers with several benefits. The growing emphasis on locating “known good dies,” which are unpackaged dies that have been tested and proved for dependability and effectiveness, has resulted in the evolution of optimal burn-in testing methodologies as well as refinement of the HTOL system. Each of the common levels has the following characteristics:
• Package-Level:
Package-level testing is a more traditional process in which dies are burn-in after they have been packed and incorporated into the finished product. While this strategy helps ensure a product’s reliability in its final phases, the cost of repairing or discarding a damaged gadget completely can be a drain on resources.
• Die-Level:
Dies are inserted and tested in makeshift carrier units before being packaged and integrated into the final product during die-level burn-in. This method lowers the cost of packaging while ensuring that only working dies are put in a device at a reasonable cost.
• Wafer-Level:
This level decreases the cost of the burn-in system process by testing wafers as soon as they complete the fabrication phase to verify component efficacy instantly. Wafer-level burn-in may produce less accurate final products than package-level procedures, but it is a more cost-effective choice.

The following are examples of a burn in testing system:
• Static Burn-In:
The testing equipment is attached to the burn-in board sockets, which are then placed in burn-in ovens where power and extreme temperatures are given during a twelve to twenty-four-hour period. After cooling, the boards are removed and the device is put through a series of functional testing. Although no external biases or loads are used to impart stress, the lack of electrical input makes the static burn-in method less effective for evaluating complicated devices.
• Dynamic Burn-In:
A device is examined at a full rate determined by the burn-in oven electronics, which can deliver power stimulation and stress to internal nodes within the device, in a dynamic burn-in system. Dynamic burn-in systems, like static burn-in systems, do not trace device reaction during stress application, which means that dies that fail cannot be recognised until follow-up functionality testing.
• Test During Burn-In:
While a device is experiencing burn-in stress, test during burn-in systems observes and applies test vectors. This method ensures that devices are switched on and that input tests are carried out as expected. Although burn-in conditions normally make contemporaneous functional evaluations impractical, downtime can be used to evaluate circuit integrity and, in turn, minimise the length of follow-up function testing.

Also, to further ripen system knowledge, learn why product testing with HAST testing, and HTRB testing is required for the production process.
Product Resilience
Unless you’re a manufacturer of appliances, for example, it’s critical to understand how your products will perform in various conditions. You should use an environmental chamber to determine how products respond to temperature, moisture, or movement.
Product Longevity
Obviously, with HAST system testing (Highly Accelerated Stress Test), you should understand how your product materials and parts will withstand humidity pressure. This allows us to assess how long buyers will be able to utilise your goods.
Quality Control
Creating a product is a complex process because one incorrect step can hurt overall performance. As a result, early problem detection in Trio-Tech International can help to avoid future complications. Early detection might also motivate you to act quickly!
Guaranteed Legit
As a company owner, you want to maintain quality to enhance your company’s reputation among consumers and other stakeholders. It’s a big duty, so employ product testing processes like HTRB system testing (high-Temperature Reverse Bias) or correct product evaluation.
Top Tier Customer Care
Anticipate that your clients continue to support your business as you develop your items. As a result, your brand’s reputation and loyalty will improve, which will assist your brand get more followers in the future. It can also improve your company’s visibility in both the domestic and foreign markets.
Finally, when more systems are added, the possibility for increased complexity grows. Technology should exist to facilitate learning, not to complicate it, and although complexity is a source of aggravation for you and your firm, it is a disaster for your customers. A quick, uncomplicated registration process should be mirrored in a smooth learning experience, ideally one that allows your students to learn on their own time and at their speed.
Ensure systematic safety for your products with test services from Trio-Tech International. Visit their website for a better product design and understanding. Collaborate with Trio-tech International, which provides product testing for improved production. It consists of top-tier system testing, HTRB testing, and HAST testing. To begin incorporating product testing into your production process, go to their webpage.
<img src=”https://i.ibb.co/k49rBXc/The-product-must-go-through-testing-for-longevity-to-guarantee-its-legitimacy.png” alt=”The-product-must-go-through-testing-for-longevity-to-guarantee-its-legitimacy” border=”0″></a>