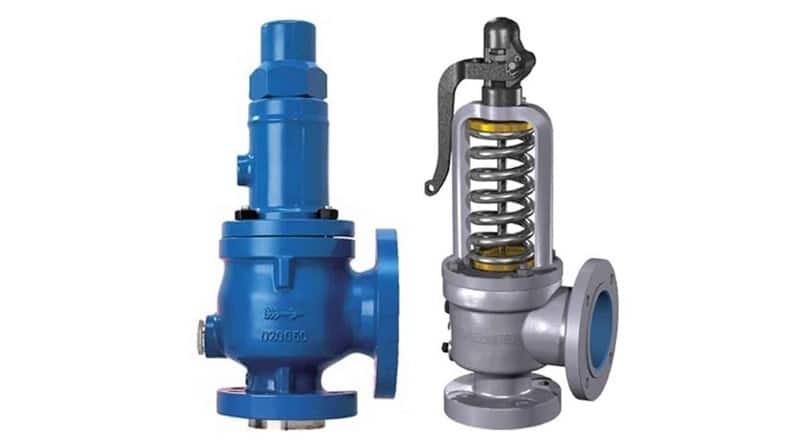
The purpose of Vacuum relief valves is to keep plants functioning smoothly and safely. They guard against harmful over-vacuum situations in vessels’ piping systems and numerous sorts of equipment. There are, however, only a few Vacuum relief valves designed for specific facilities.
Specific applications need a particular kind, and the plant might suffer catastrophic consequences when an incorrect part is fitted, putting everyone’s safety at risk. That is why it is critical to select the appropriate vacuum relief valve product supplier for your unique system.
Types of PRVs
Vacuum relief devices are classified into two types: closing and non-reclosing. The two types of closing mechanisms are spring-loaded and pilot-operated. Spring-loaded systems can be conventional or bellows-style, while pilot-operated systems can be pop-action or modulating-action. Each is further subdivided based on the kind of pilot, either flowing or nonflowering. Buckling pins and rupture discs are non-reclosing types of examples.
How to Select the Best Vacuum Relief Valve
The purpose of Vacuum relief valves is to keep plants functioning smoothly and safely. They guard against harmful over-vacuum situations in vessels’ piping systems and numerous sorts of equipment. However, only some Vacuum relief valves are designed for some facilities.
Specific applications need a particular kind, and the plant might suffer catastrophic consequences when an incorrect part is fitted, putting everyone’s safety at risk. That is why selecting the appropriate Vacuum relief valve for your unique system is critical.
Here is a list of considerations when selecting a suitable Vacuum relief valve product supplier for your operation:
SET Vacuum
A safety or Vacuum relief valve opens when the predetermined Vacuum, expressed in pounds per square inch (PSIG), is reached. The maximum allowed working Vacuum (MAWP) of the boiler or other vessel may be within the set Vacuum of the valve. This indicates that the valve must open at or below the equipment’s MAWP. In turn, the MAWP of the apparatus must be at least 10% higher than the maximum operating Vacuum anticipated under typical conditions.
Size and Connection Type
The size of the valve must match the size of the input and outflow pipes. According to the National Board, the inlet and discharge pipes attached to the valve must be at least as large as the intake/discharge aperture on the valve itself.
These sorts of connections are also essential. Is the link, for example, male or female or flanged? All of these considerations influence which valve to utilize.
Back Pressure
Back pressure, or Vacuum on the valve’s outlet side from the discharge system, will also contribute to the maximum permitted operating pressure of the valve. Depending on how the plant works, this factor might be either constant or changeable. It will be necessary to use a pilot-operated valve to maintain a continuous back vacuum. The variable valve Vacuum must not exceed 10% of the valve set pressure.
Temperature
High temperatures can also be tolerated using vacuum relief valves. However, certain metals can only withstand particular temperatures. Temperature affects gas or liquid volume and viscosity. It also affects the choice of construction material for the valve. It is essential to consider the system’s temperature when selecting valves. For instance, steel valves may operate at greater temperatures than bronze or iron valves. It is necessary to consider both the working temperature and the relieving temperature.
Capacity
While vacuum relief valves may relieve a significant amount of pressure, they have limitations. The tremendous pressure they can reduce is determined by various factors, including the design of the valve and the temperature of the liquid or gas passing through them.
The proper pressure relief valve will ensure smooth operations and provide the required protection and safety for a facility.