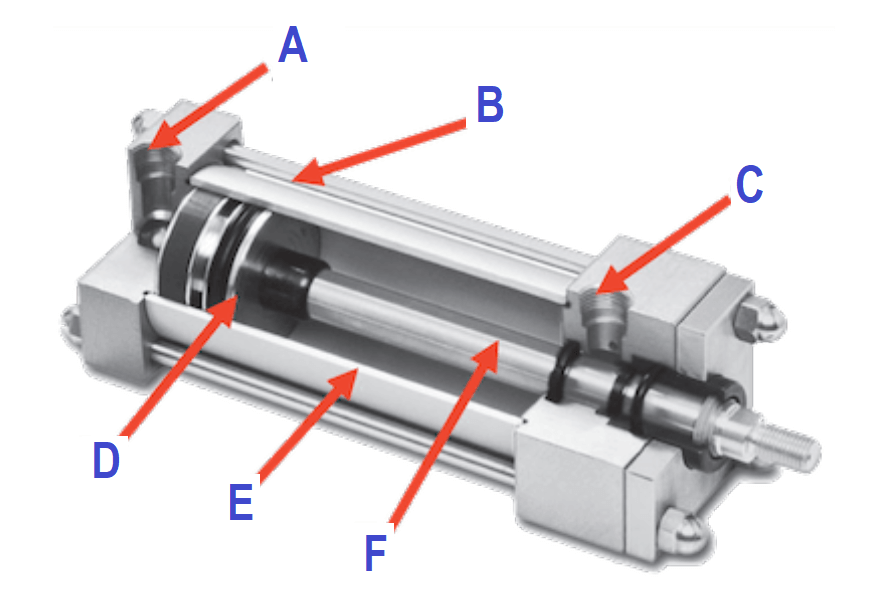
Correct maintenance of the pneumatic system is essential to maintain continuous operation, reduce energy costs and prolong component life. Although pneumatic equipment is generally very reliable compared to hydraulic or electrical equivalents, these systems still need to be properly maintained. Negligence in the correct maintenance of the pneumatic system can cause serious future problems for your application.
Preventive and corrective maintenance programs are essential to managing equipment life cycles, with the ultimate goal of reducing downtime and protecting people and machines from damage.
Preventive Maintenance In Pneumatics
Doing maintenance before you have problems is one of the best ways to reduce expenses and eliminate downtime. The pneumatic system needs to be maintained regularly, depending on the manufacturer’s recommendations, the peculiarities of the equipment, and the frequency of use. With this information, it is necessary to create a preventive maintenance program, with actions, persons responsible, and dates for repairing the pneumatic system.
The main preventive maintenance action in pneumatic automation is to ensure air quality
It is essential to check that the filters are working correctly and clean or change them regularly. Also, it is essential if the line has small leaks and eliminate them.
A simple tip for creating the preventive maintenance program is to read the system manually, understand the circuit and the particularities of the components. The manual usually points out the critical areas for proper system maintenance.
Corrective Maintenance On Pneumatics
Corrective maintenance is undesirable and happens when we have a system failure. Even in a simple pneumatic connection, a small failure can lead to very costly downtime for operation or even accidents. To alleviate problems in case of failure, it is possible to take some steps:
- Have replacement stock of the most common items
- Survey of parts and codes used in the system
- Suppliers with fast service and stock
- Use quality parts
Maintenance Tips
Safety First
The first tip in pneumatic maintenance, and one of the most important, is to ensure that the system is entirely off without air pressure.
Cylinders can move, causing accidents and equipment damage; unconnected pressurized hoses can cause whiplash and also cause damage. It is essential to have a latching block valve to prevent unexpected system pressurization. The soft-start valve can also ensure smooth pressurization when the system is pressurized again.
Culture Of Eliminating Air Leaks With Routine Inspections
Audio/visual inspections are the most effective ways to diagnose and prevent problems with pneumatic systems and their components.
Pay close attention to the noise of air leaks. It’s easy to hear when air leaks, especially when the plant isn’t running and the system is already pressurized. It is essential to correct this leak to avoid problems and reduce compressor usage, no matter how small. In addition, simply walking around the equipment and visually detecting things like loose and broken parts or worn hoses is the first step to effective maintenance.
The equipment operator must be familiar with all components of the pneumatic system, especially the connections that deserve more attention.
Compressed Air Quality
Poor compressed air quality is one of the biggest reasons for problems in pneumatic systems. The compressor and piping of the pneumatic installation can generate a lot of waste and water that can condense and oil generated by the compressor.
It is essential to have a good air preparation system with drains, filters, regulators in all production cells. We often see that the air preparation unit is not serviced properly, causing damage to the components ahead.
It is necessary to check the filter drain cup and that the filter element is in good condition. Also, check that the air inlet to the filter is clean and free of residues.
Connections
Pneumatic quick-connect connections are cost-effective and straightforward. Replacing them can be done quickly. That’s why it’s essential to have a stock of connections available; it’s essential to reduce downtime. Connections are often a source of leaks in applications. That’s why it’s essential to use quality fittings, which hold the hose firmly and release easily.
If you need to repair cylinders for heavy machinery, get in touch with professionals.